ARGO 2.0 MULTICAMERA STAR TRACKER
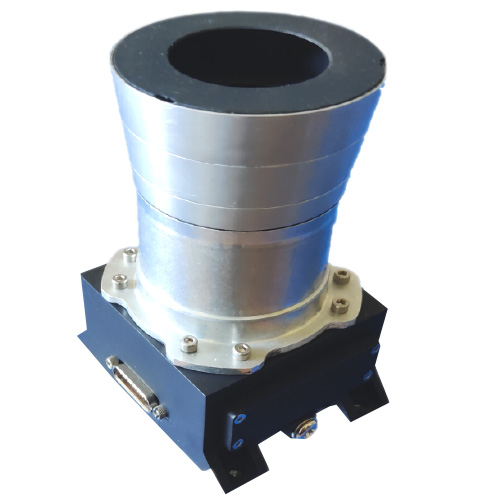
The star tracker ARGO 2.0 intends to be a ‘smart redesign’ of the ARGO 1.0 architecture, targeting as main features:
1. a further reduction of mass and power consumption, keeping the performances as close as possible to current architecture’s
2. a seamless integration with the platform control, assuring high stability and maneuverability for microsats platforms.
In fact, a drastic reduction of SWAP will make this solution more suitable for future large constellations.
- Multiple optical heads (OH) including a pre-processing SW,
- data fusion software – to be partially embedded in the Satellite Onboard Computer (OBC). Such a SW will be able to perform the fusion of data coming from the two optical heads, in order to get attitude and rate measurement, and to perform the auto-calibration of both camera model and camera relative attitude. Alternative, a specific Data Processing Unit (DPU) can be provided for up to 3 OH.
ARGO 2.0 will determine the attitude with respect to the Boresight Reference Frame (BRF) of one of the Optical Heads, to be rigidly mounted to the payload of which the attitude has to be measured. The other OHs can be mounted as preferred by the user. ARGO 2.0 output includes:
- attitude of one OH, assumed as a reference (quaternion from fused raw data).
- angular speed.
- angular acceleration.
- OH’s updated calibration models (all cameras).
- relative attitude of the other OHs with respect to the Reference one;
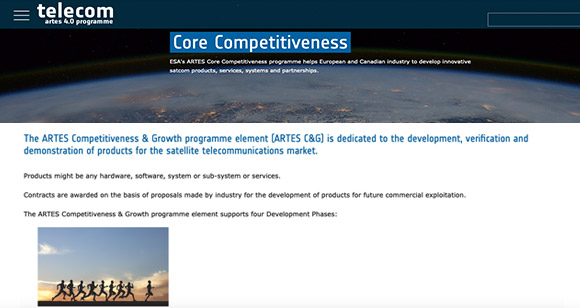
On March 2020 the Team has been awarded by the European Space Agency a grant for the development, qualification and in-orbit demonstration/validation of the ARGO 2.0 star tracker (“ARGO 2.0 for Constellations”, ESA Contract 4000130361/20/NL/MM/ra, ARTES Competitiveness & Growth Programme).
The Project started on April 2020. During 2020÷2021, EICAS worked with its partner TSD Space to the ARGO 2.0 design.
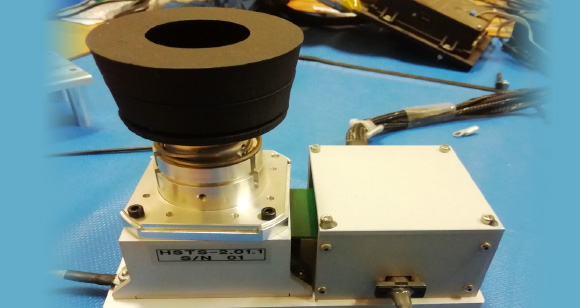
ended in ____ April 2021
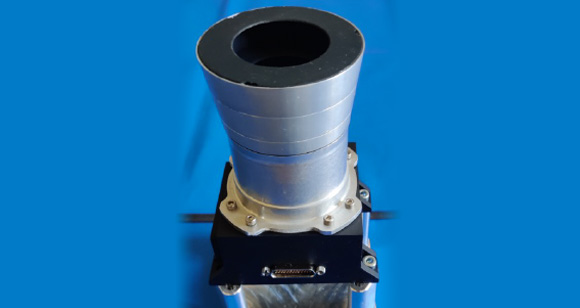
May 2022 ____ Present
ARGO 2.0 ENVIRONMENTAL TEST CAMPAIGN
ARGO 2.0 OH Qualification Model is undergoing the environmental test campaign. Radiation tests were successfully performed on the optical elements and the electronic components, while vibrations and pyroshock tests were successfully executed on the Qualification Model. In the following months the Team will carry out the Thermal Vacuum Tests and the Electro-Magnetic Compatibility (EMC) tests, so completing the on-ground qualification campaign.